ノイハウゼン工房本格始動
ケースとムーブメントパーツの新たなる製造拠点
シャフハウゼンに拠点を構えるIWC。
しかしケースとムーブメント製造部門の大部分は、近郊のノイハウゼンに移転した。
新工場の完成に伴い、パーツの内製率をいっそう高めたIWC。
そこで見たものは、いかにもIWCらしい、品質に対する厳密さであった。
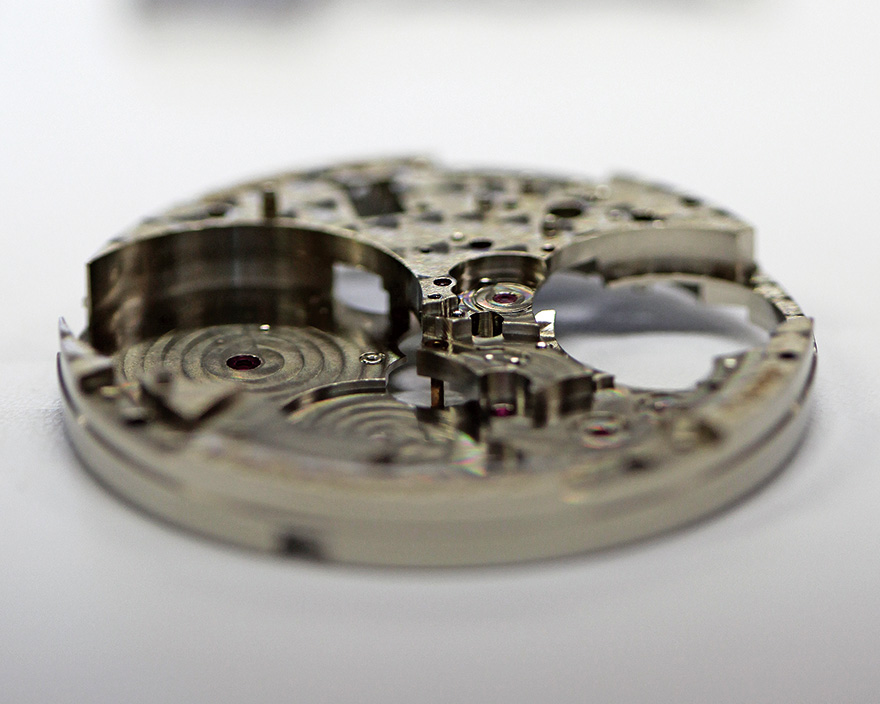
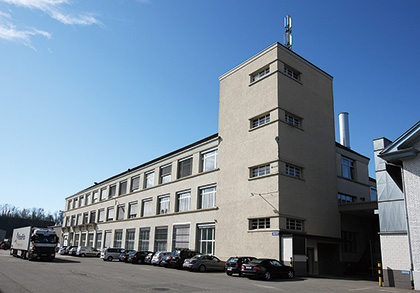
筆者はひとつ大きな誤解をしていた。ここ10数年、IWCは巧みなマーケティングで業績を伸ばしてきた。その一方で、肝心の時計作りがおざなりになったという印象が、どうにも拭えなかったのだ。しかしノイハウゼンの新工場を見る限り、それは杞憂であった。ややもすれば華々しいマーケティングに隠れてしまいがちだが、手堅い時計作りというIWCの本質は、まったく変わっていなかったのである。
IWCの製造部門は、シャフハウゼンから近郊のノイハウゼンに移転を始め、2011年にそれを完了させた。まだペンキ跡も生々しい新工場(取材時)では、パイロット・ウォッチを含む、ほとんどの時計のケースとムーブメント部品が製造されている。
1980年代に入って、IWCはチタンケースの自製に取り組んだ。以降同社は、チタン加工のノウハウを生かして、ゴールドやSSケースも社内で加工するようになった。2004年の時点で、ケースの内製率は約50%であった。しかしノイハウゼンの新工場落成により、内製率はほぼ100%に近くなった。
鍛造されたブランク(ケースの大まかな素材)を購入し、自動機械で切削(ミリングとドリリング)を加えた後、研磨して仕上げるというプロセスは他社と同じだ。しかしIWCは専用の機械を使って、完成したケースの表面粗度を厳密に計測している。5個ないしは10個にひとつ、表面の粗さを計測し、基準内に収まったものだけを出荷する。筆者はさまざまなケース工場を見て回ったが、ここまで厳密に計測するのは、IWC以外にない。
またIWCのケースは素材も異なる。現在パイロット・ウォッチのSSケースは、日本製のステンレス素材から加工されている。加工部門の責任者曰く「他社の素材に比べて高価だが、日本製のスティールは例えばドイツ製のそれに比べてス(泡状の傷)が入りにくい」とのこと。比較のため、他社の素材で試作したケースを見せてもらった。確かに磨いたラグにはスが入っている。しかし日本製の素材には、ほとんどスが入らない。
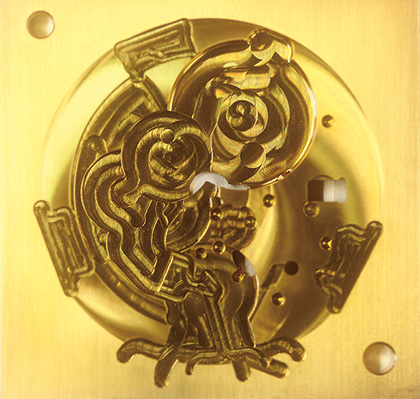
ケースの内製化に伴い、細々とした付帯作業もノイハウゼンに移管された。一例が裏ブタへの加工である。現在IWCは、裏ブタへの刻印をケミカルエッチングで行っている。かつては外注だったが、「質を上げるため内製に切り替えた」という。まだ裏ブタへの刻印が浅いと指摘したところ、現在「深くできるように改善中」との答えが返ってきた。「深くすると刻印の周囲が荒れてしまう。しかし深くできるようにトライ中だ」。すぐ改良できるのも、内製化のメリットだろう。
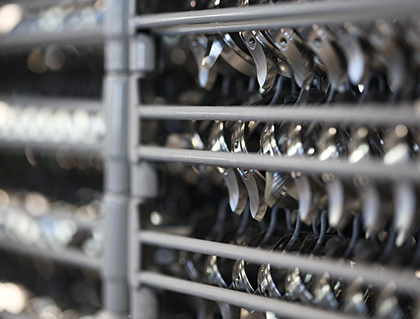
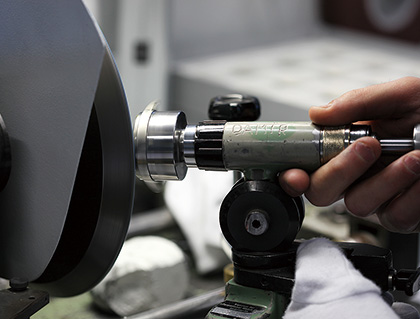
ノイハウゼンでのケース製造は、スイスの他社同様、高度に機械化されている。ブランクを多軸CNCにセットすると、自動的に加工され、ある程度のケースができあがってしまう。しかしケースの磨きやクリーニングには、30人もの人間が携わっている。ビッグ・パイロットを例に取ると、3枚の紙やすりを使い分け、40分の時間をかけてサテン仕上げを施す。今や多くのメーカーは、ケースの磨き工程も自動化しようと試みている。しかしノイハウゼンの工場には、多くの熟練した磨き職人が在籍する。
デザイナーのクリスチャン・クヌープ氏はこう説明する。「かつてのパイロット・ウォッチは、作りやすいデザインに特徴がありました。ミリタリーウォッチであるということは、作りやすさと同義語ですね。でも現在のパイロット・ウォッチは造形が複雑になり、立体加工が必要となりました。また仕上げにも、サテンやグロスを併用するようになりました」。パイロットウォッチを特徴付けるサテン仕上げが、手作業でしか施せない理由だ。仮にケースの造形を簡潔にして、全面をポリッシュ仕上げにするなら、磨きの工程を機械化できるだろう。しかし「マスキュリンでテクニカル」(クヌープ氏)というパイロット・ウォッチの個性は失われるに違いない。
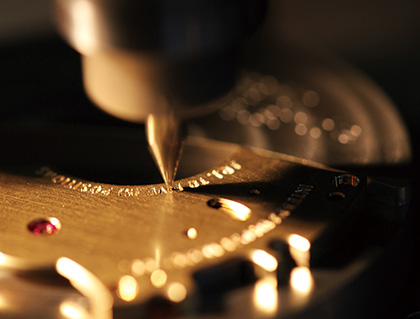
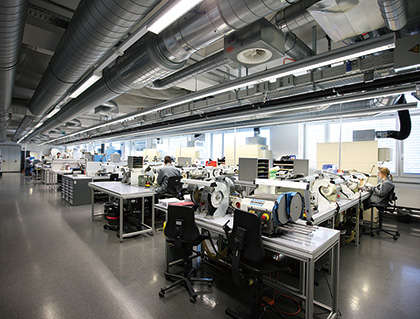
ケース製造部門の奥には、ムーブメント部品の製造部門がある。CNCや放電加工機といった設備は他社に同じだが、いくつか面白い機械を見た。ひとつがペルラージュ用の機械である。現在IWCは一部のモデルに他社のエボーシュを使っている。通常エボーシュに、特別な仕上げを施すことはありえない。しかしIWCでは、この機械を用いてエボーシュの地板にペルラージュを加え、また刻印機を使って、自社のムーブメント名を刻印する。コストを考えればそもそも無駄な作業だし、一部の例外を除いて、他社ではこういった手間を加えない。決して手間を省略しないのが、いかにも老舗ではないか。

現在、リシュモン傘下の各社は、急速に生産設備を集約化している。例えばケースの製造はドンツェ・ボームに、ムーブメントの製造はヴァル フルリエにといった具合だ。もちろん製造コストは下げられるが、よほど上手くコントロールしない限り、時計メーカーとしての個性は失われてしまう。対して高い内製率を誇ってきたIWCは、ノイハウゼン工場の落成によって、それをいっそう引き上げようとしている。好調な売り上げがあればこその試みだが、正直言うと、ここまで内製化が進んでいるとは想像もしていなかった。
ここ10数年で、良くも悪くもパブリックイメージを大きく変えたIWC。しかし新しい製造拠点であるノイハウゼンで見たものは、昔と変わらぬというよりも、いっそう手堅くなった、時計作りへの姿勢であった。とりわけ、あえてコストのかかる作業を残しているのが、いかにもIWCではないか。何が他社との差別化になるのか。IWCというメーカーは、それを十分知悉して、ノイハウゼンの生産ラインを整えたに違いない。