超難切削材に挑むリシャール・ミル専任の自社ケース工房
リシャール・ミルの共同設立者であるドミニク・ゲナ氏が率いる自社ファクトリー「オロメトリー」に続いて、2013年に設立されたリシャール・ミル専任のケース工房が「プロアート・プロトタイプス」である。極小生産を得意としてきた小工房を母体とするここで、ゴールド素材以外のほとんどが“超難切削材”となるリシャール・ミルのケースが生み出されている。
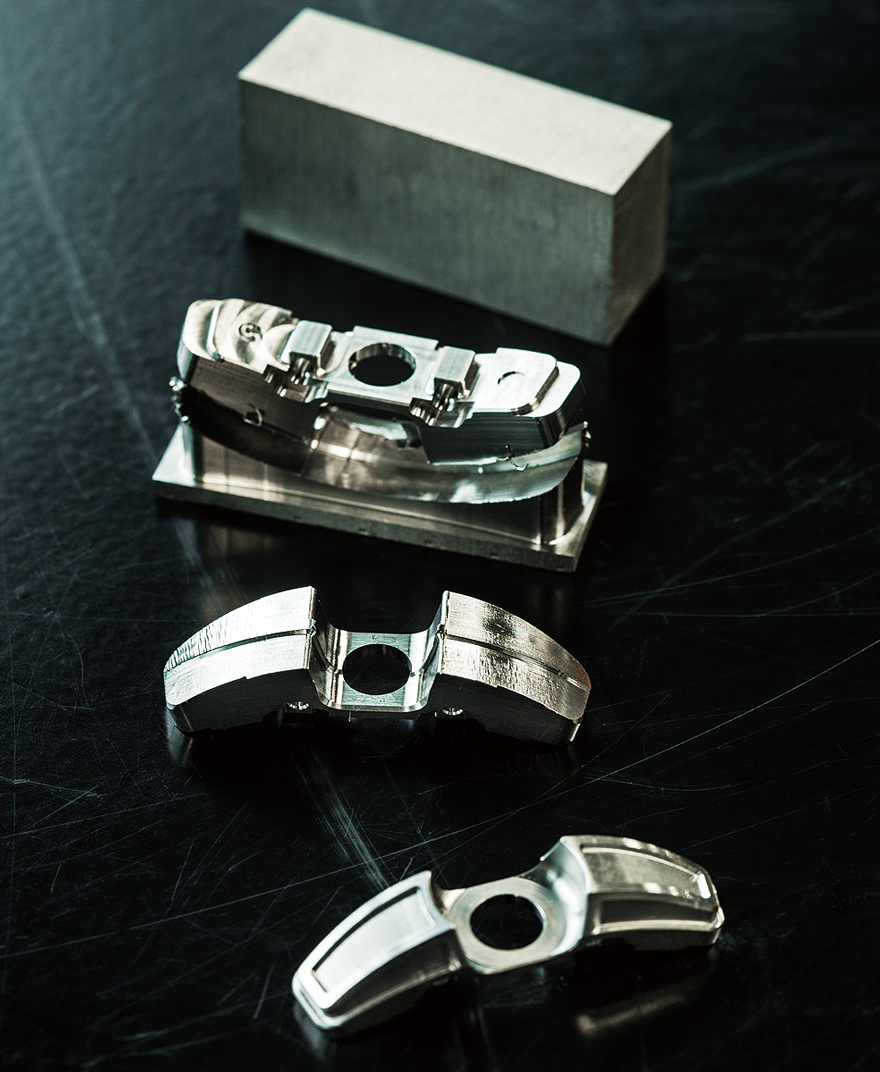
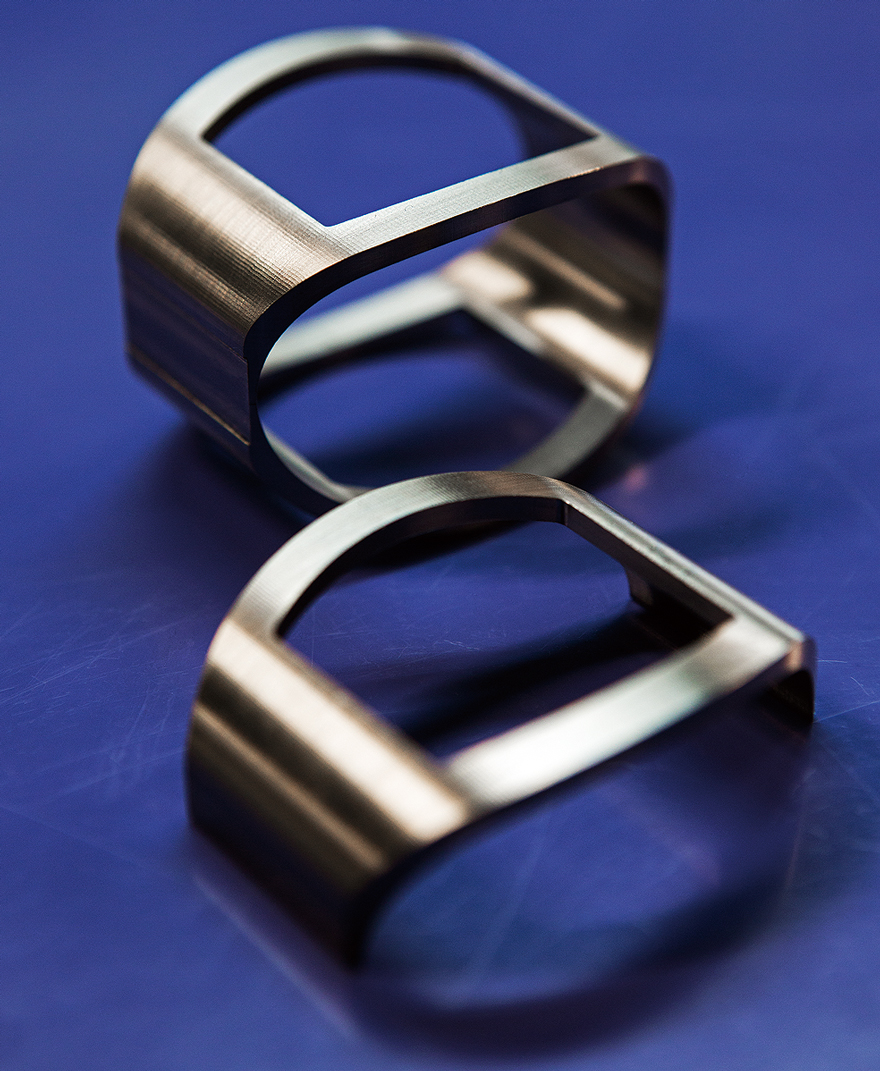
独創的なムーブメントの開発と同様、リシャール・ミルの革新性の中心となっている特殊なケースマテリアル。その製造を担う、最も新しい拠点が「プロアート・プロトタイプス」である。もともとかなり小規模だった独立系のケースサプライヤーを、リシャール・ミルの共同設立者であり、同社製造部門のひとつである「オロメトリー」の代表も務めるドミニク・ゲナ氏が拡大。2013年からリシャール・ミル専任の自社ケース工房となっている。
約30名のスタッフを抱えるここは、年産数約3000個(当然ながらRMの年産数と同数)とキャパシティは決して大きくないが、切削加工に特化したCNCは最新の機材が投入されている。例えば5軸フライスのスピンドル回転数は、一般的な4万rpmに対して5万rpm。取り扱う材料が超難切削材ばかりのため、そのノウハウも独特だ。例えばカーボンやチタンの切削時には、まるで滝のように切削油を吹き付ける。切削時に発生したバリを洗い流しつつ、ツールや母材の温度を少しでも下げることが目的だ。さぞや歩留まりも悪かろうと思ったが、切削パス生成などの製造前シミュレーションを厳密に行うため、それほど歩留まりは悪くないという。ただしゴールドなどに比べて、チタンやカーボンは切削ノウハウが確立されていないため、事前調整にかかる時間は膨大だ。
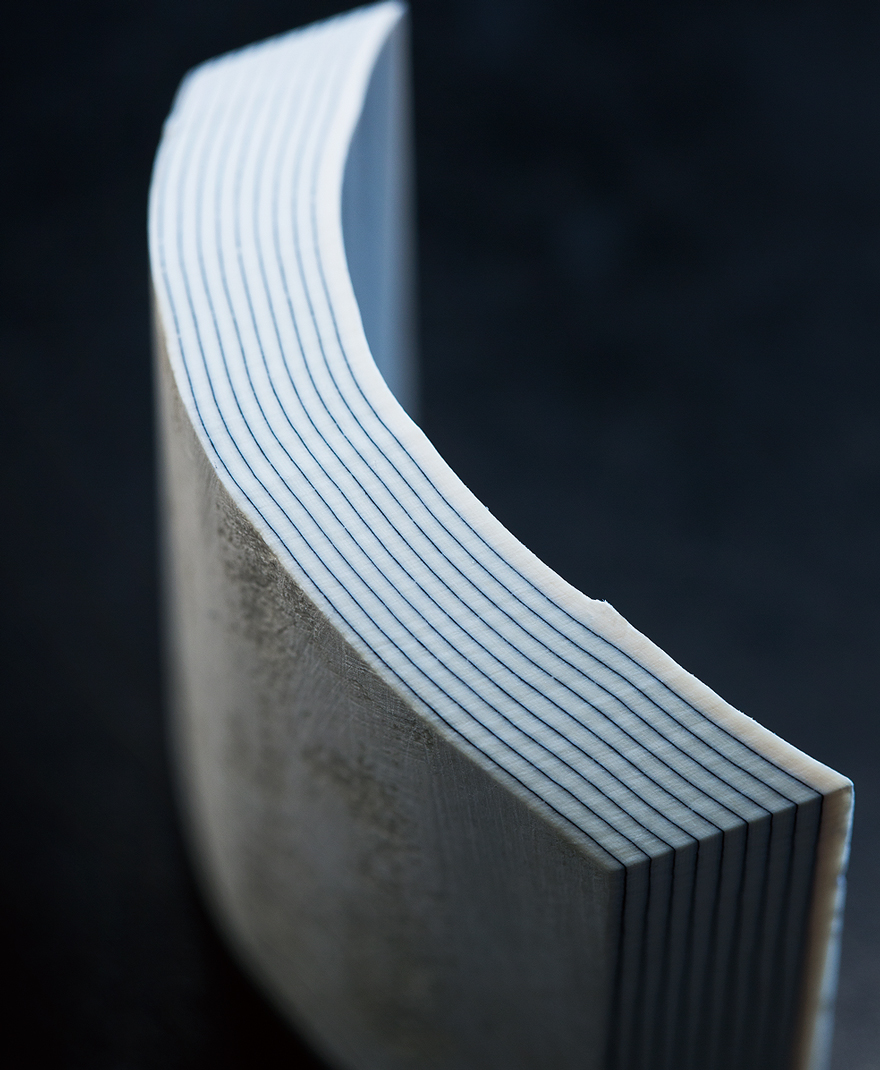
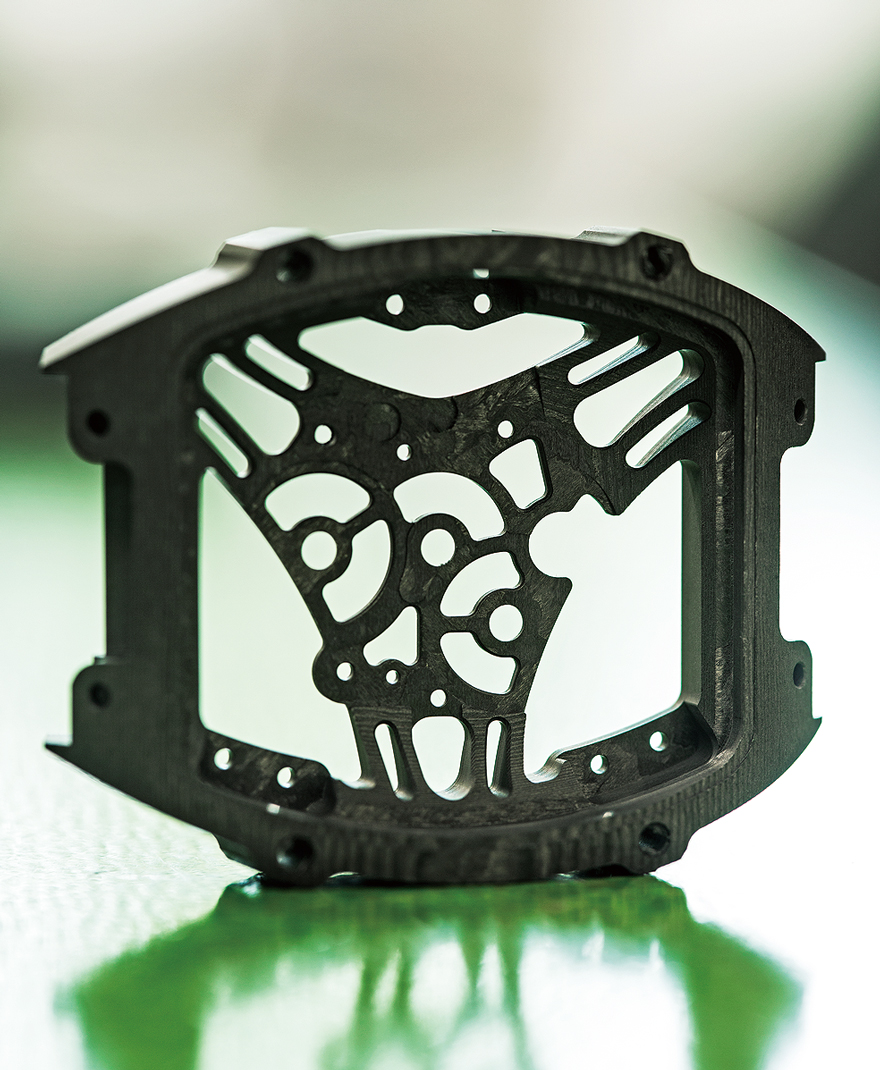
また、約1年前に新規導入されたという接点センサーを用いるQCも厳格。ケースの仕上がりチェックならば100分の1ミリ単位が普通だが、プロアートではムーブメントパーツと同様に、1000分の1ミリ単位でチェックする。そのチェック箇所は、ベゼル1枚で100箇所にのぼる。最終的には、工房にひとりしかいないというフィニッシャーの手仕上げを経て、特殊素材のケースは完成へと至るのだ。
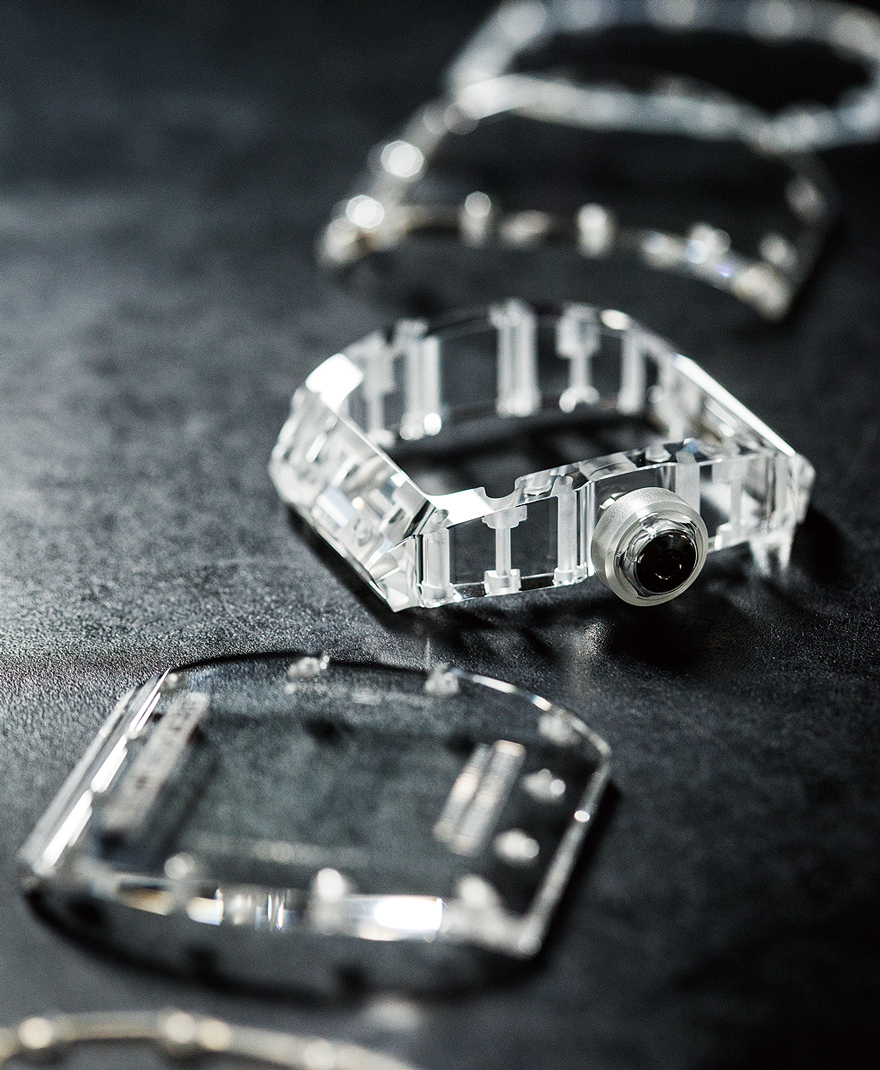
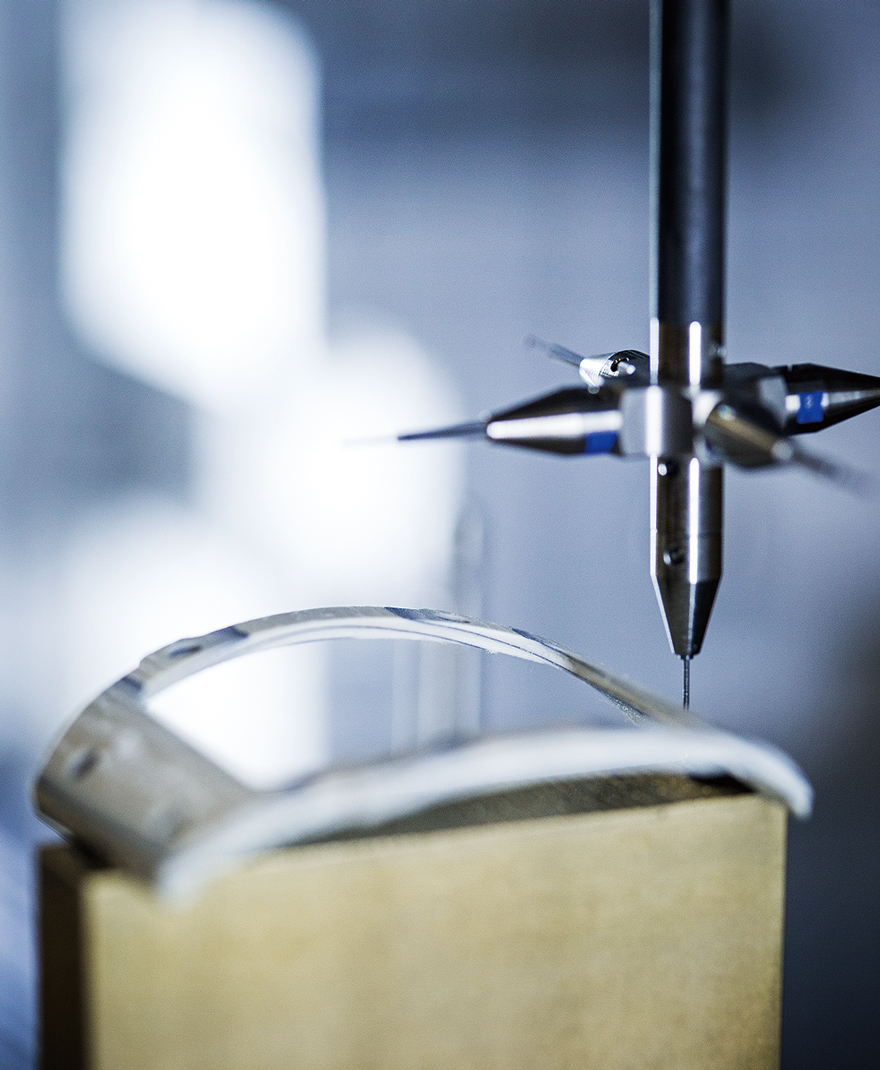