近年、時計市場に普及する“新素材”。外装やムーブメントに従来にはなかった素材を用いることで、時計は形状や色といった意匠の面ではもちろん、性能面でも大きく変化した。『クロノス日本版』112号で「時計を変えた新素材」として、そんな“新素材”を特集した記事を、webChronosに転載する。第1回は、「時計素材の原点」であるゴールド製の高級ケースの製造を行う独立系サプライヤー、スティラを取り上げる。
Photographs by Yu Mitamura
鈴木裕之:取材・文
Edited & Text by Hiroyuki Suzuki
[クロノス日本版 2024年5月号掲載記事]
伝統的な技法をベースに進化を重ねる時計素材の原点
スイス時計産業のバックヤードを支えてきた外装系のサプライヤー。その中でもケースを手掛ける独立系の工房は、最盛期の200~300社から、大メーカーによる吸収や統廃合を経て、現在はスイス全体で15社ほどにまで数を減らしている。残った彼らが目指すのは、クォリティの徹底したハイエンド化だ。ラ・ショー・ド・フォンの独立系工房「スティラ」の仕事をサンプルに、最も伝統的なマテリアルであるゴールドケースの最新事情をレポートする。
独立系工房「スティラ」が手掛けるゴールドケース
スイス時計産業の黎明期から用いられてきたゴールドケース。その源流は、16世紀末の宗教弾圧でジュラ山脈のスイス側に移り住んだ時計職人たちの技術と、宝飾や工芸の盛んだったジュネーブの金銀細工師たちの技術が融合したことに始まる。この特集は、2000年代以降に主流となったニューマテリアルに焦点を当てることが本義だが、それらが生まれる土壌となった伝統的なマテリアルにも目を向けておきたい。サンプルは、ゴールド製の高級ケースに特化したラ・ショー・ド・フォンの小工房「スティラ」だ。
筆者がこの工房を訪れたのは2023年の秋頃。ちょうどコロナ禍の影響が過ぎ去り、各社がオーダーを倍増させてきたタイミングだ。44名のスタッフを擁し、大手ブランドとハイエンドの独立時計師を合わせた22社からの発注を請け負うここでは、過去3年で生産数が約3倍に跳ね上がったという。コロナ禍で中間価格帯の需要が落ち込み、ハイエンドマーケットのみが好況に沸くという状況の中で、要求されるクォリティのレベルは大きく跳ね上がった。リファレンスとなるのはやはりパテック フィリップ。現在はすべてのブランドが、パテック フィリップと同質のケースを求めているという状況だ。そうした中でスティラでは、素材そのものの粗度にまで注意を払って、溶接やポリッシュを行っている。
まずはお馴染みのCNC切削。ブランク材のゴールドをいかに少なくオーダーできるかが腕の見せ所だ。約40種のヘッドを駆使する旋盤加工では、ダイヤモンドカットを入れただけで鏡面に近い仕上がりが得られる。「完成パーツのような状態が我々のスタート地点。これが現在のスイスの底力だ」と言うが、これはその後の仕上げを入れやすくするための下準備でもある。
なぜスティラが切削精度にこだわるのかと言えば、ここで作られるケースの9割以上が、ラグを別体で作ってロウ付け(溶接)しているからだ。ロウを施す断面のアールがきちんと揃っていないと、溶接自体が難しくなる。電気溶接の際に用いるハンダが弾けるようなことも稀に起こるという。
ラグ位置を固定する電気溶接に用いられるのは、ジグそのものが電極となっている自社開発の特殊工具。位置決めのためのハンダ付けを1回、さらに低温ハンダによる仮付けを1回行ってから、本格的なロウ付けが始まる。筆でプロテクションを塗りながら、位置決め用のハンダで出来たケースとラグの僅かな空間に、本付けのロウを流し込むのだ。ロウを流したらケースごとオーブンに入れ、750〜890℃の温度でロウを溶かして溶接する。もし仮付けが甘ければ、この熱でラグ位置がずれて、全てが台無しになってしまう。
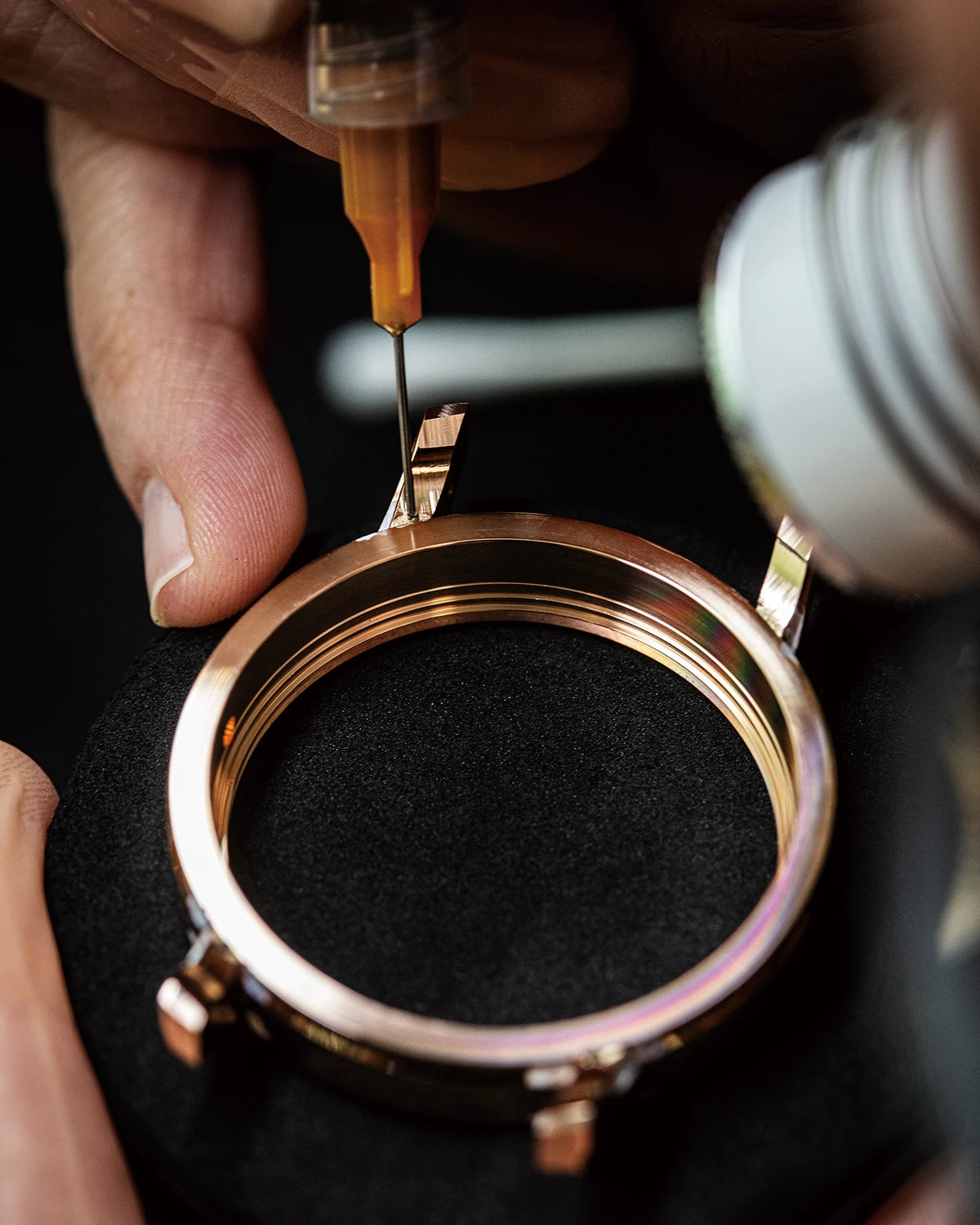
また、ゴールドケース表面の粗度は細かければ細かいほど良いと言うが、オーブンに入れることで若干だが荒れる。表面の粒子が粗くなると、金サビのようなオレンジ色の染みが生ずることもあるため、母材である5Nゴールド(赤色の18Kゴールド)の品質にまで気を配る必要がある。スティラが用いる5Nゴールドのレシピは、厳密に言えばミドルケース用とラグ用で若干変えられているため、表面の粗度も異なっている。それが原因で時には溶接が巧くいかないこともあるというが、それを解決するのがノウハウだ。またコルドン(コードの意味)と呼ばれる溶接痕は、本来ラグの全周にあることが理想だが、これを好むメーカーと好まないメーカーがいる。どちらにしても、溶接ビードのようなひと目でそれと分かるような痕は、時計のケースには存在してはならない。もっとも現在では、別体のラグをロウ付けすような、昔ながらのハイエンド工房は少なくなっており、溶接技術者は社内で育成してゆくしかないのだという。
スティラでは、自社製のゴールドケースに用いるケーシングリング(ムーブメントリング)も自製している。丸棒切削で作られるケーシングリングの素材は、かつては真鍮製が主流だったが、近年では医療用のクロム材(クロムコール)に置き換わっている。これは静電気の発生を抑制し、吸収することが目的で、簡易的な耐磁ケースの代替にもなるという。保護ではなく吸収。サファイアクリスタルバックの時計が、一定の耐磁性を確保できるのは、このあたりにも理由がありそうだ。また小ロット生産のケース組み立てに用いるパッキンも、ジュラコン素材の削り出しで自製している。ユニークピースやハイエンド向けのケース製作も、かつては年間20個程度だったが、現在は約120個。その需要は5〜6倍というスケールに跳ね上がっている。
以前はスイス全体で、スティラのような独立系のケースサプライヤーは200〜300社ほどもあった。しかし現在では15社程度。スティールケースではキャパシティ面での競争力勝負になるから、こうした腕のあるサプライヤーは、ハイエンド向けの貴金属ケースに特化するようになってきている。またアジア諸国に流れてしまったロジスティクスが、コロナ禍の影響で再びスイス国内に集約されるようにもなってきた。大規模ケースサプライヤーや、内製化を進めたハイエンドブランドでは、ケースのポリサージュまで自動化したがる傾向にあるが、スティラではそれは無理だと断言する。「素材は生きているから、毎回変わる」。段階的なチェックを入れながら、ひとつずつ工程を積み重ねてゆくのが、ハイエンド工房たる所以だろう。